MK33 | High speed blister packaging machine with plate sealing
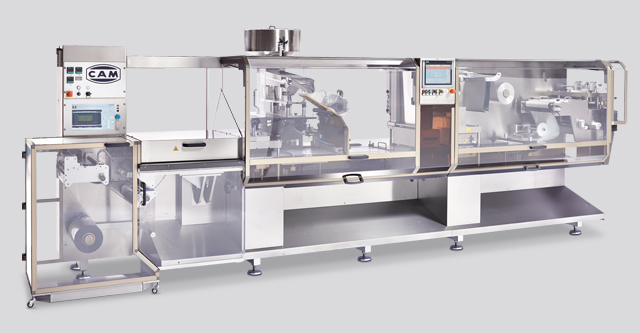
Machine working flow
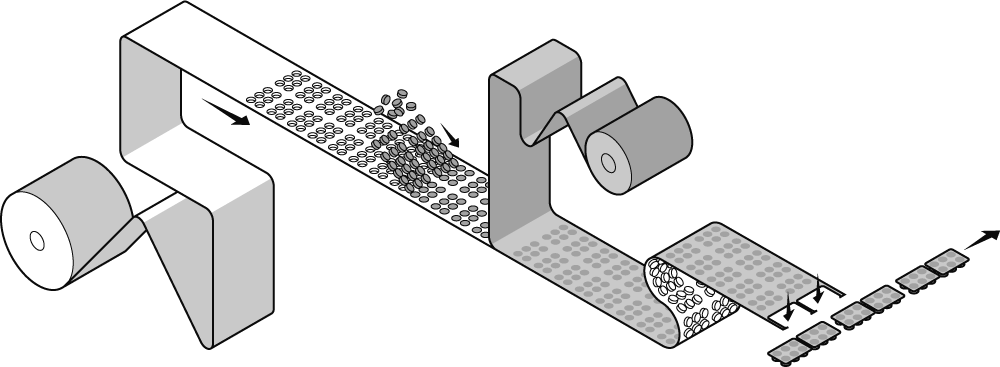
Description
Blister packer model “MK”
Designed and constructed in accordance with the requirements of the Pharmaceutical Industry and in observance of GMP standards, the MKblister packaging machine has maintained the principal characteristics which distinguish CAM blisterpackers.
Simplified use and ease of cleaning
The path of the web between the reel and forming material and the cutting station is as short and linear as possible giving the operator full vision and total control of all the principal functions of the machine. The above together with a careful design study which has separated the areas enclosing the mechanicat movements from the areas dedicated to product handling, enable line clearance and machine cleaning upon batch change-over to be carried-out with simplicity and ease. Format change-over can be carried-out by the use of quick release devices, even by unskilled personnel.
Flexibility / versatility
The machine can handle a wide range of forming materials, such as: PVC, PP, PVC- PVDC, PVC-PE-PVDC, ACLAR, PETG, ALLI-PE, ALU-PP and lidding materials such as: ALUMINIUM, ALUMINIUM- PAPER, ALUMINIUM-PAPER-MYLAR, ALUMINIUM-PE, POLYPROPYLENE. Owing to the cornplete range of feeders available, the machine can handle products such as hard or soft gelatine capsules, round and oval sugar coated pills and coated or uncoated tablets of any shape and in any different presentation
Heavy-duty structure and mechanical reliability
According to the dimensions of the product, the machine can produce up to 12 blisters/stroke (up to 4 along the web and 3 across). Web transfer is carried-out by 4 mechanical grippers, the third of which acting directly on the housings, guaranteeing (with the use of any type of material) correct positioning of the formed stroke between the sealing station plates. The intermittent motion of the web is generated by a mechanical crank and slotted link device in conjunction with the motion of the feeders. The relationship between these two movements allows the housings to be loaded even during web stand-by, giving the possibility to feed product (into the housings) during the whole cycle. Feeding throughout the complete cycle and the possibility to have up to 3 blisters across the web, allows to reduce the feeding speed of each single product lane, with obvious advantages in terms of reliability and maximum performance. From the cutter (operating without creating crossways waste), blisters are transferred to the connecting conveyor, placed at 90° to the machine. This allows different linkage solutions with the downstream equipment including the possibility to install the blister packaging machine in an environment separate from the rest of the line. Upon request, the machine can be pre-arranged to accept change parts of former machine models.
Packed products
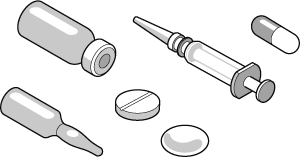
Machine layout
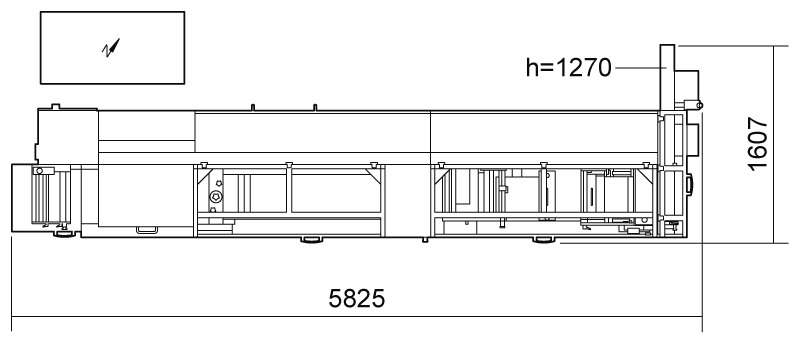
Size range
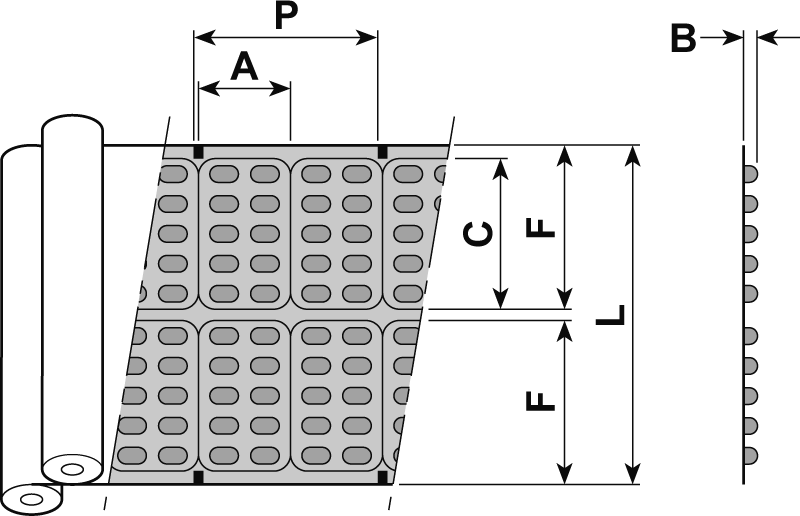
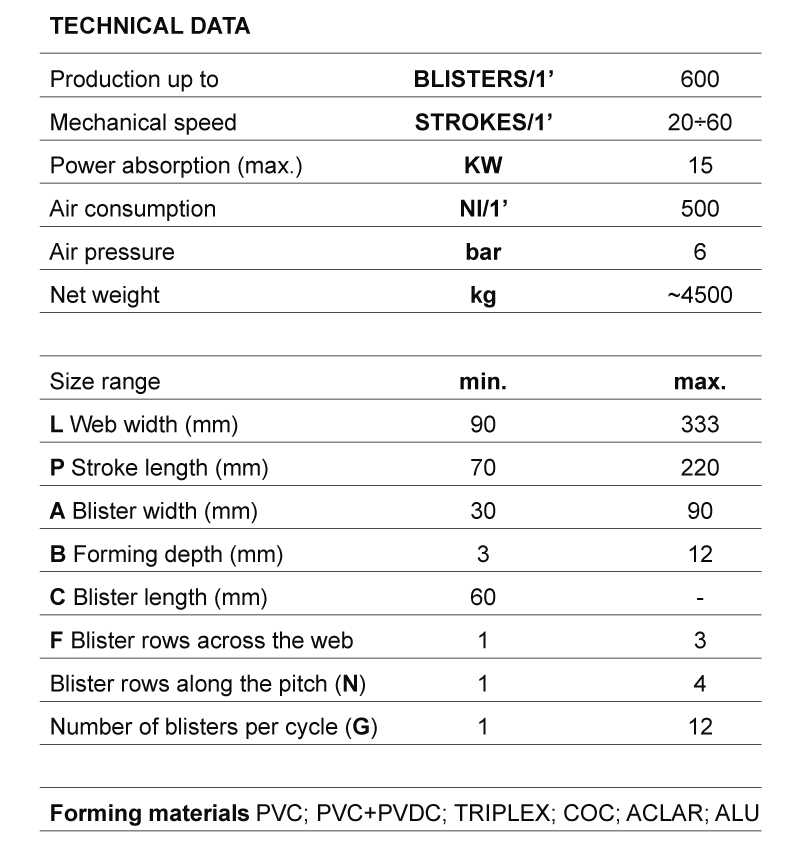